We can machine your brake rotors in house while they are still attached to your car. So what? Is there an advantage? PICTURES BELOW: Very much. 99% of the other repair shops in Deland have to take your brake rotors off and send them out to a machine shop to get them cut/turned. This creates a delay in speed of repair. And even more than that, the accuracy of the machining is greatly diminished by removing the rotor off of the car. Now you've changed the rotor mounting which allows new factors to come into play. When you cut a rotor while its still mounted to the car, you have 100% of the accuracy in the original mounting the rotor will be used upon daily. No new factors come into play. You don't have to remove the bearings, repack the bearing with new grease or replace the seals. You don't have the dismantle and replace time involved and you don't have the travel time in dropping off or picking up the rotors from the local machine shop. These are great savings in time and money while the quality is actually being improved. There is no downside except the expensive purchase price of the machine which has stopped the other 99% of car repair shops in Deland from getting one. It takes 10 years to recoup the investment and ours is finally paid off and actually pulling a profit for us. Now to keep it running for 10 more years. We do virtually all the HONDA brake rotors in Deland because they have such special crushed packed bearings it is nearly impossible to get them off without destroying them and then increasing the cost of the brake job with the additional bearing costs which sometimes can cost more than the brake job. 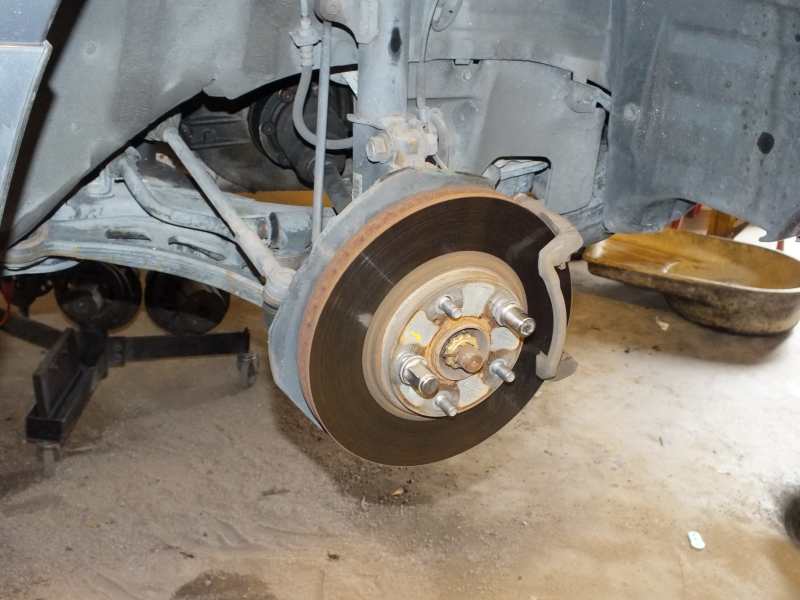
Now we are starting with a very well used brake rotor in need of maintenance. Specifically it needs to be evened out in the width department so its width is exactly the same in every location. After much use they can develop thin and thick places where they are no longer the same width in all locations(they don't always wear evenly). The brake pads grab the thick places more and the thin places less and this creates a vibration that can be felt when your applying your brakes. Also the smooth glaze needs to be removed back to raw metal without a glaze. 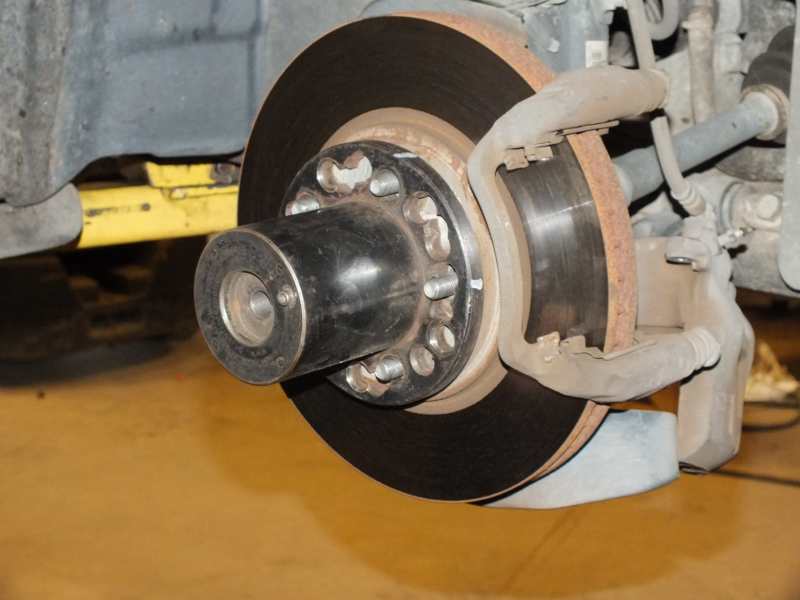
Now this is the very special but funny looking machine that will cut the high/thick places of the rotor down to match the thin places so it becomes perfectly even again. 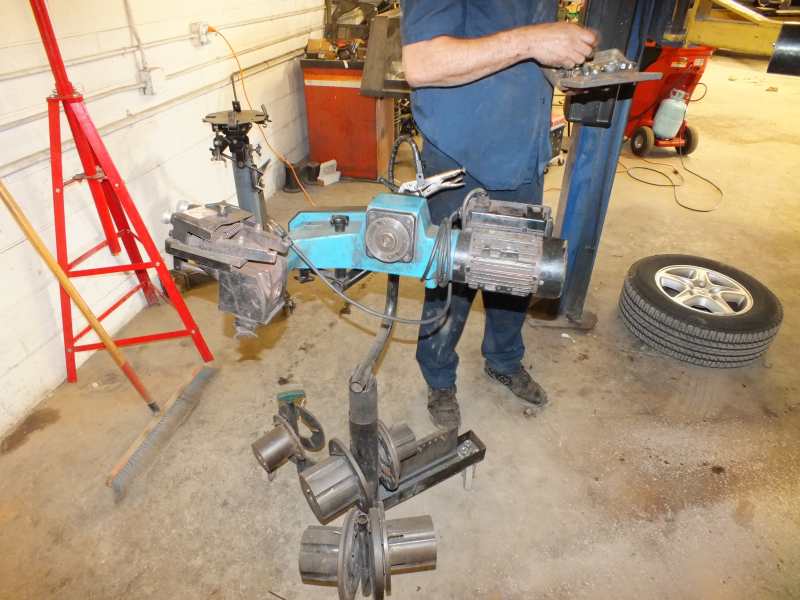
Below the machine you see several very special adapters so it can be connected to all makes and models. 
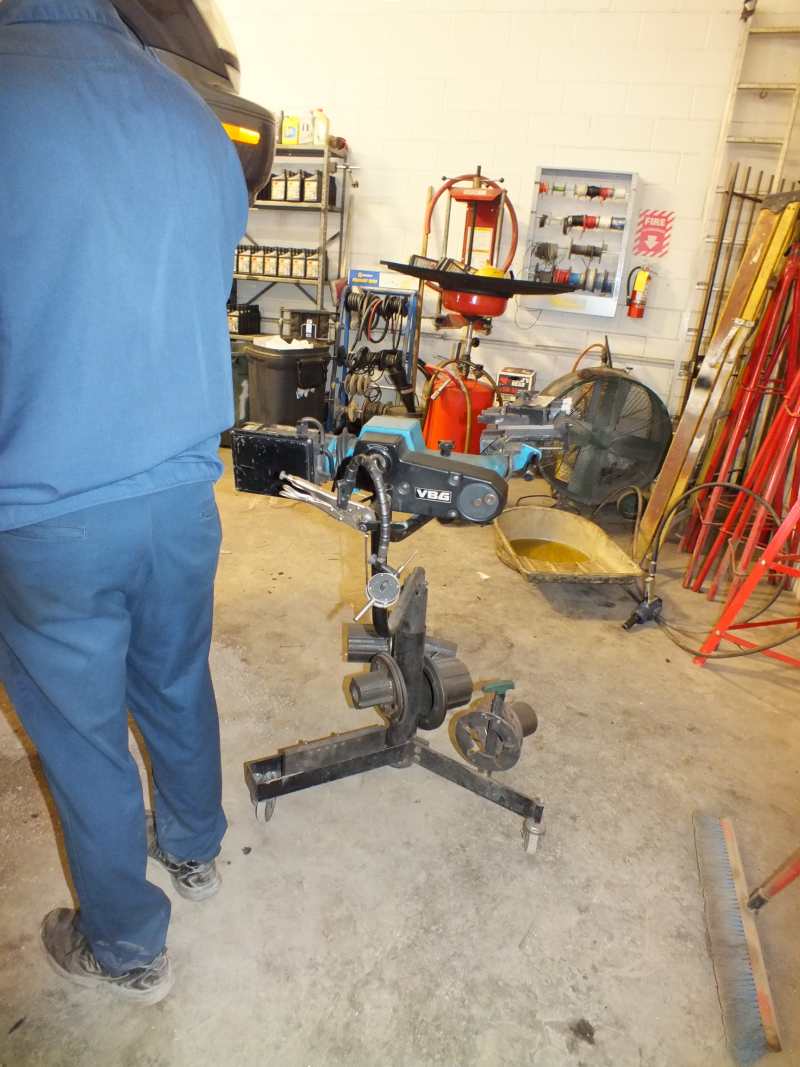
Judd is mounting one of the adapters to the rotor which the machine will then mount to. 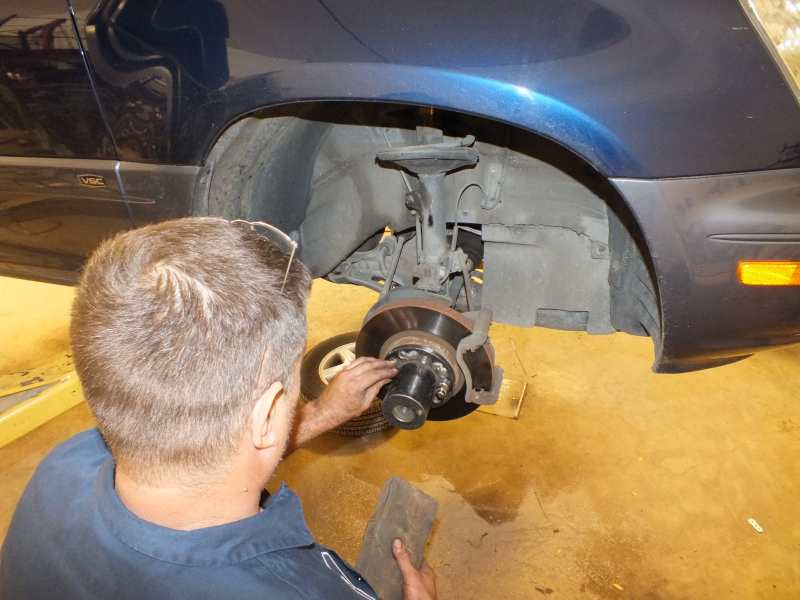
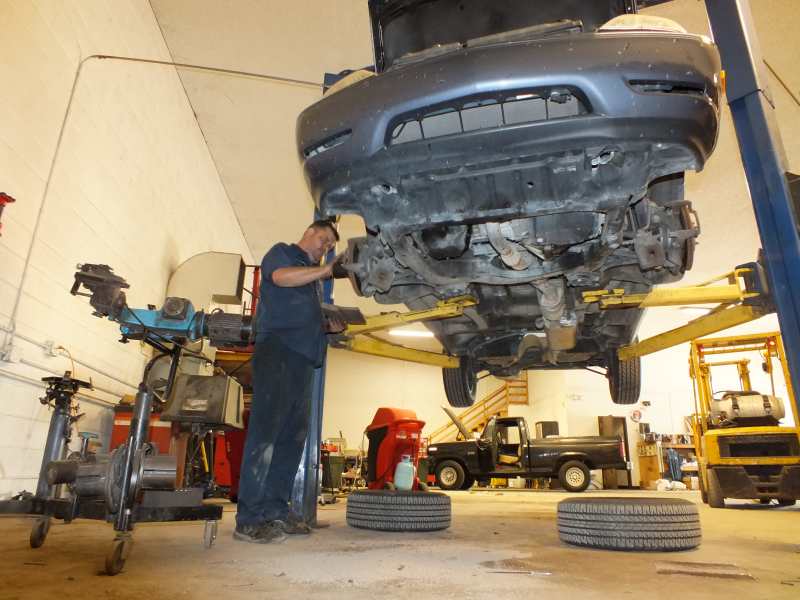
Tightening that adapter upon the rotor. 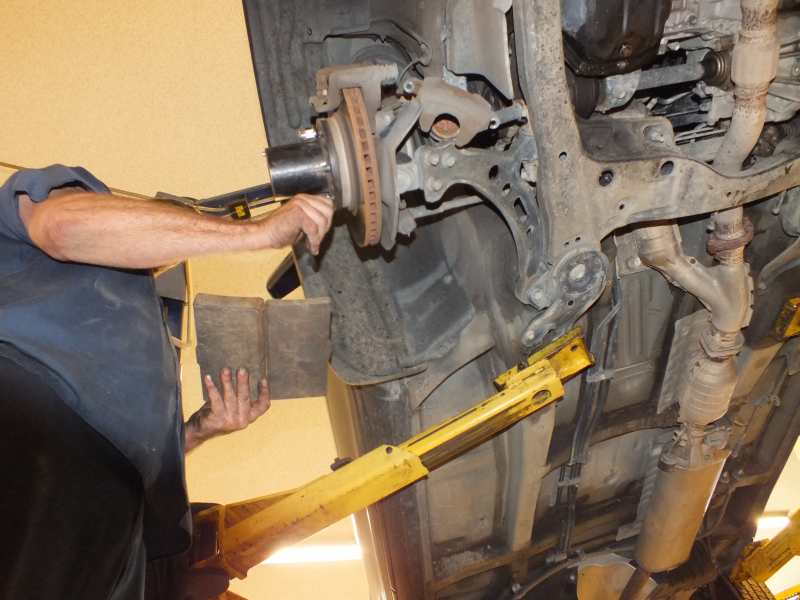
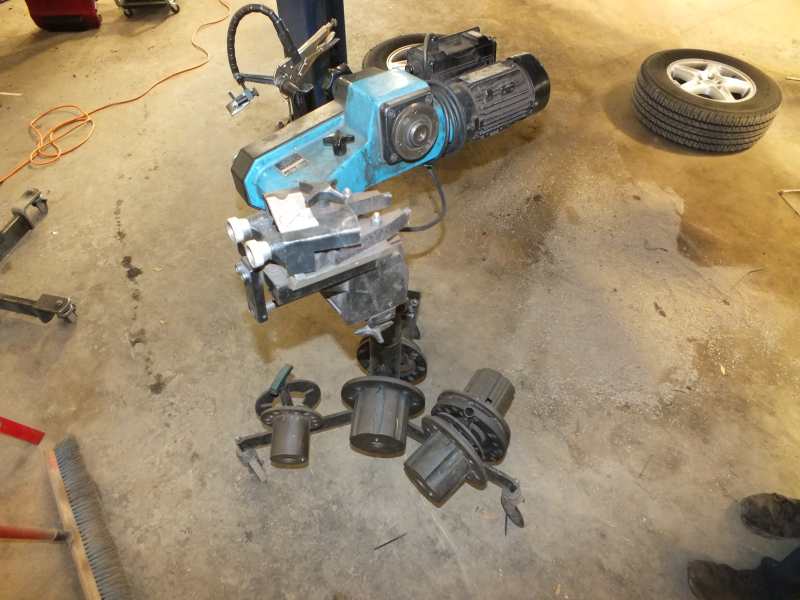
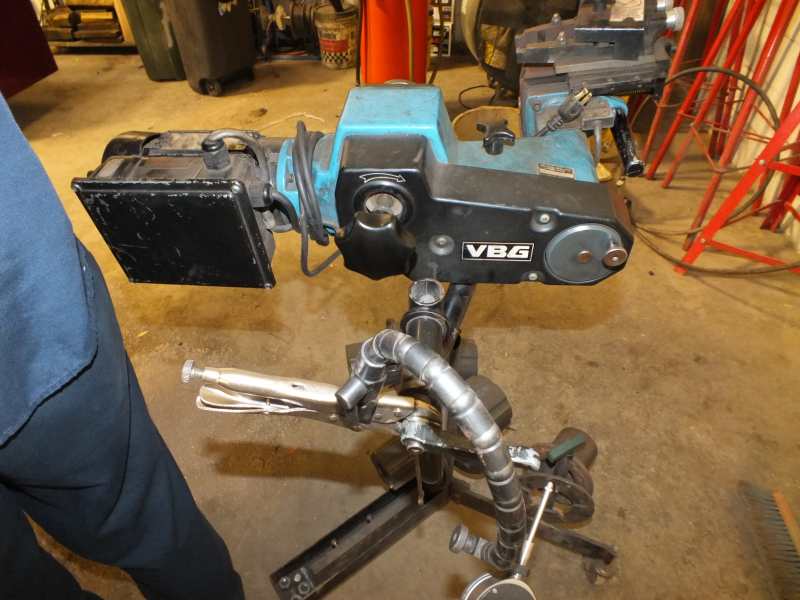
Now Judd is connecting the machine to the adapter mounted upon the rotor. 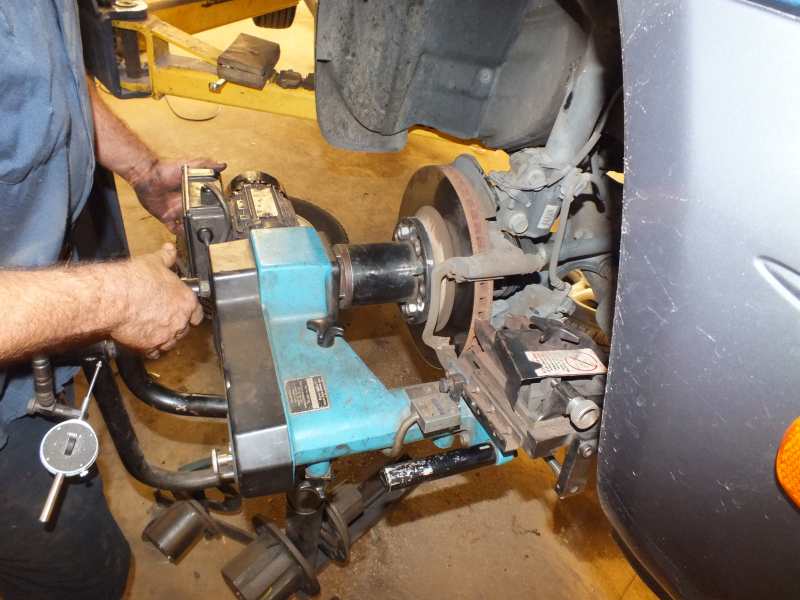
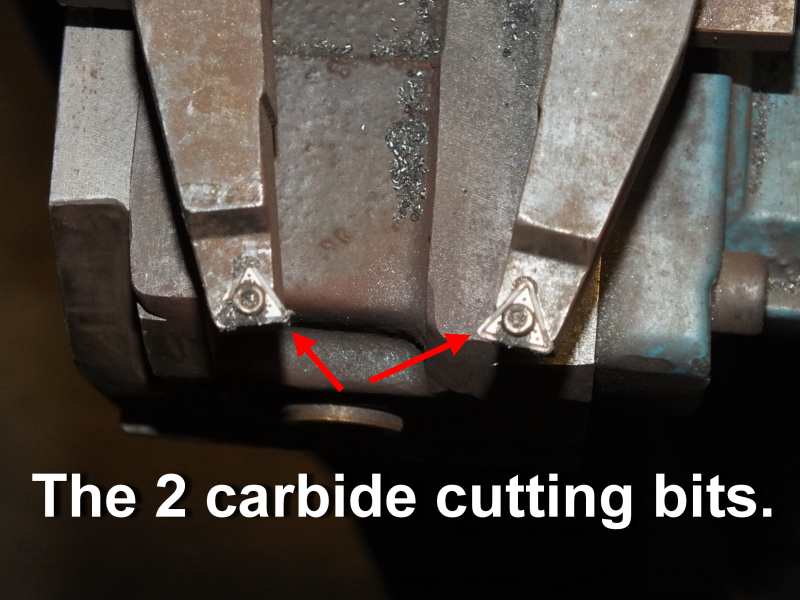
While the machine will cause the rotor to rotate and spin, the machine also controls the two cutting bits so they chew/grind/cut the rotor down evenly and precisely. 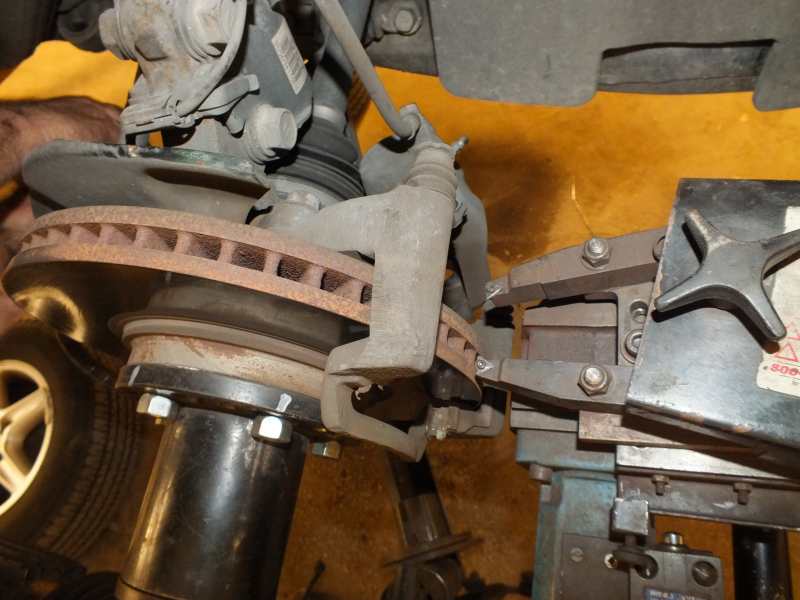
After the machine is mounted to the rotor that it will turn and cut, the machine needs to be calibrated to that exact rotor ROTATING set of characteristics. This means it is set up to match your automobiles characteristics exactly. 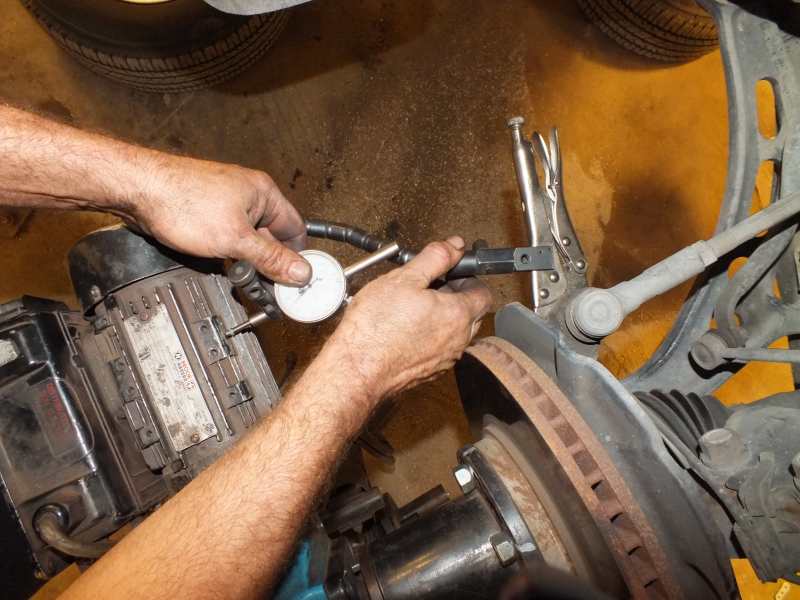
Now the machine can identify if the rotors axis of rotation has a wobble in it as compared to its mounting on your car frame and this can be adjusted to. Here is where a machine shop falls short as they cant monitor the rotation axis as it compares to the frame of your automobile. They cant get the rotating feedback that we can. But we can. And we do. And we compensate for any variables that aren't supposed to be in our perfect world but yet do exist. Since we can identify it we can work around it to create the long term solution. 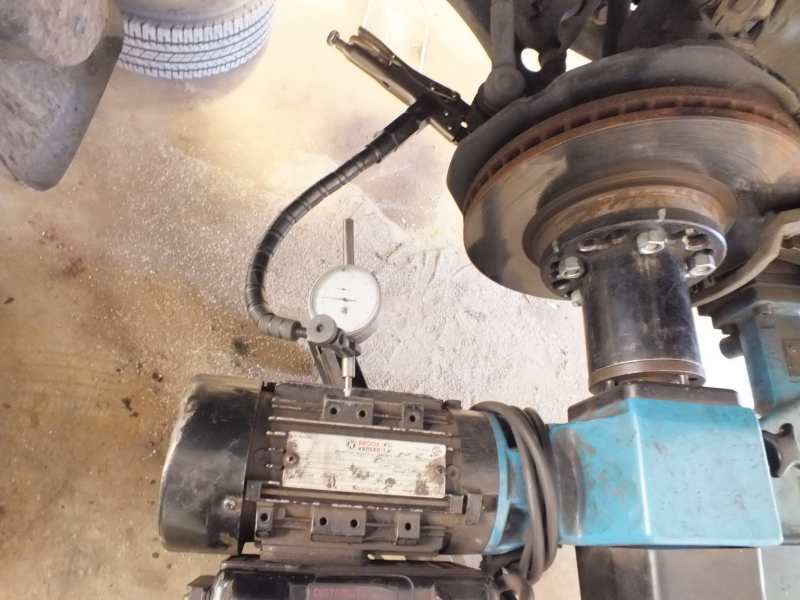
The accuracy of this machine is absolutely amazing when compared to what a machine shop delivers as their finished product. We blow em totally out of the water. A machine shop delivers their rotors with plus or minus 20 thousandths of an inch. That's a lot of play. We can tune it down to get from 2 thousandths of an inch, all the way down to 1/2 of a thousands of an inch. 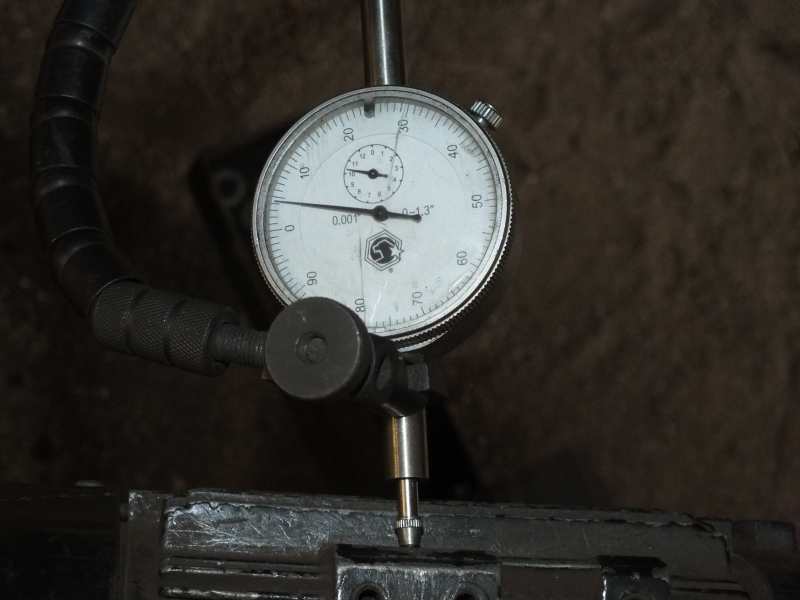
Where the arrow starts out on the meter is NOT relevant. How much fluctuation positive or negative the arrow moves while the machine is spinning is relavant 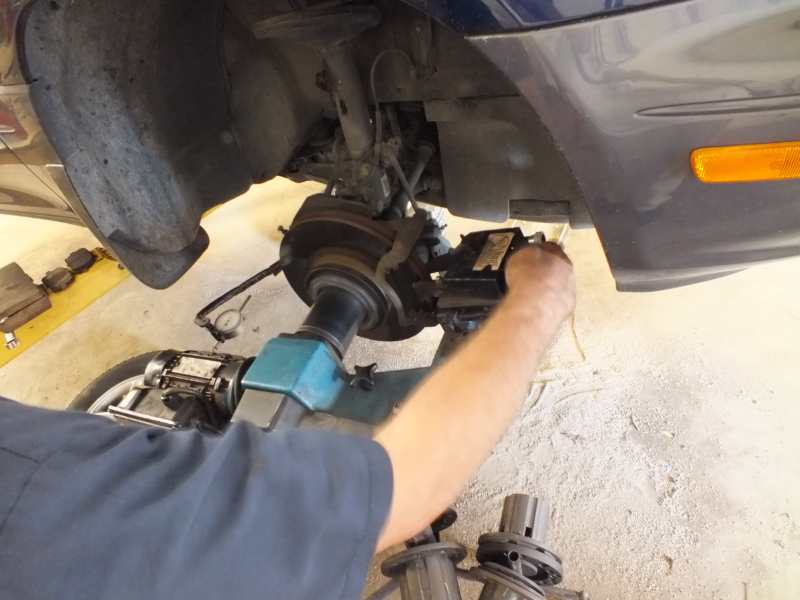
Now we are calibrated and its time to cut the rotor down. When I don't use the flash on the camera, you can see the spinning motion in the still picture. 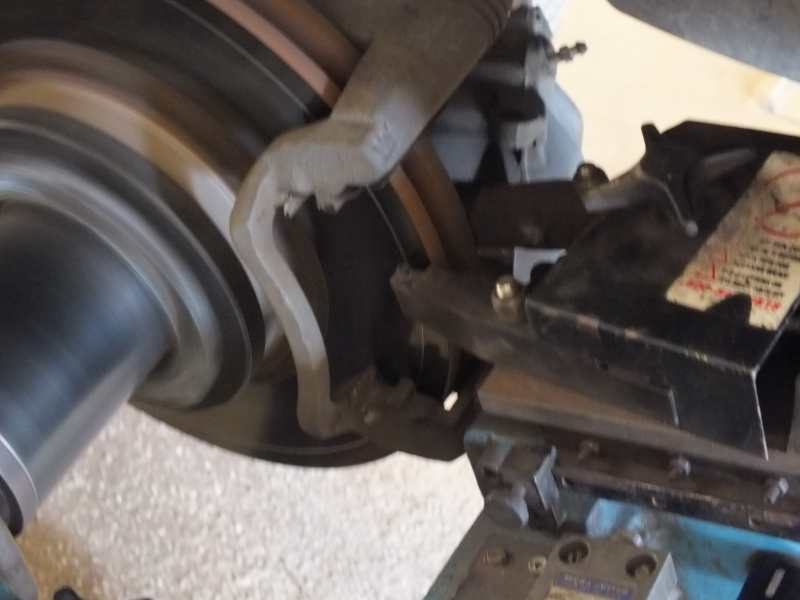
When I do use the flash on the camera, it freeze frames all the motion and you can even see it capture the flying shards of cut metal flying through the air off the carbide cutter blades as they contact the rotor removing metal. 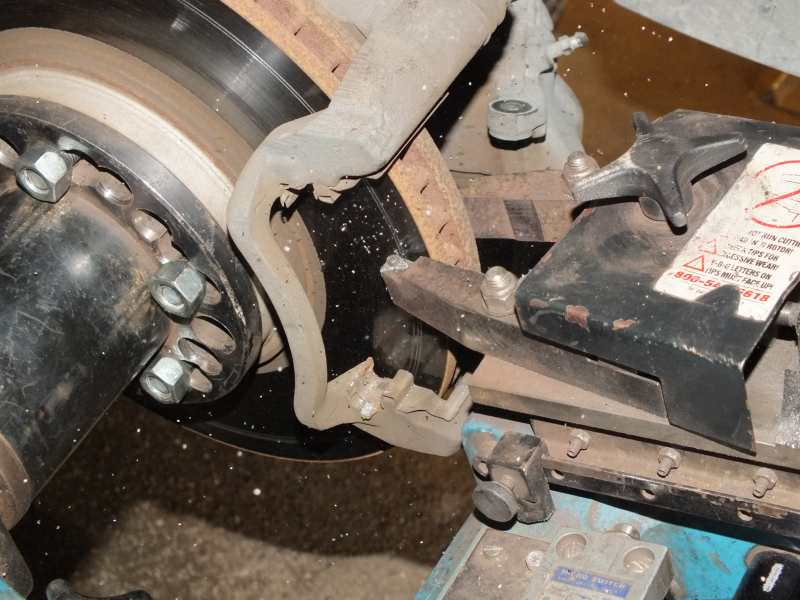
Judd begins from the outside cutting a spiral path to the center as he analyzes the shape of the rotor. 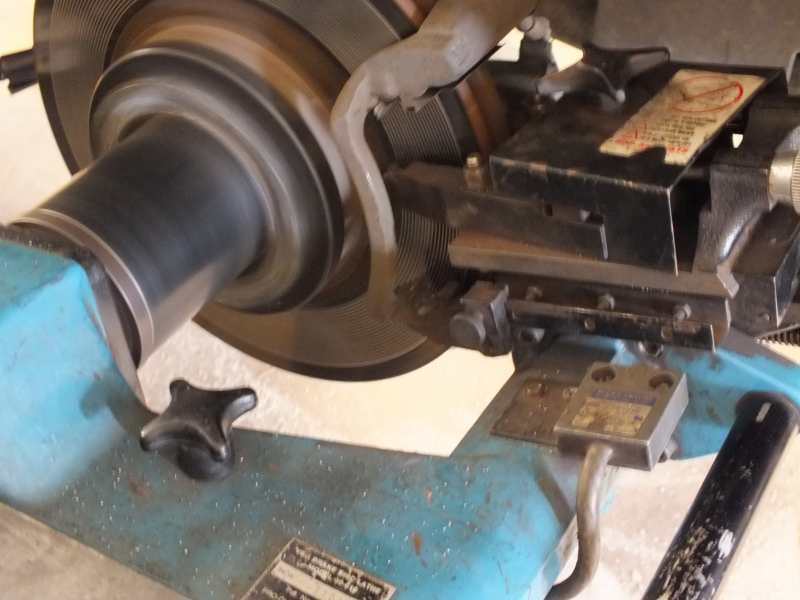
You can see the spiral path cut similar to threads on a bolt but not as deep. 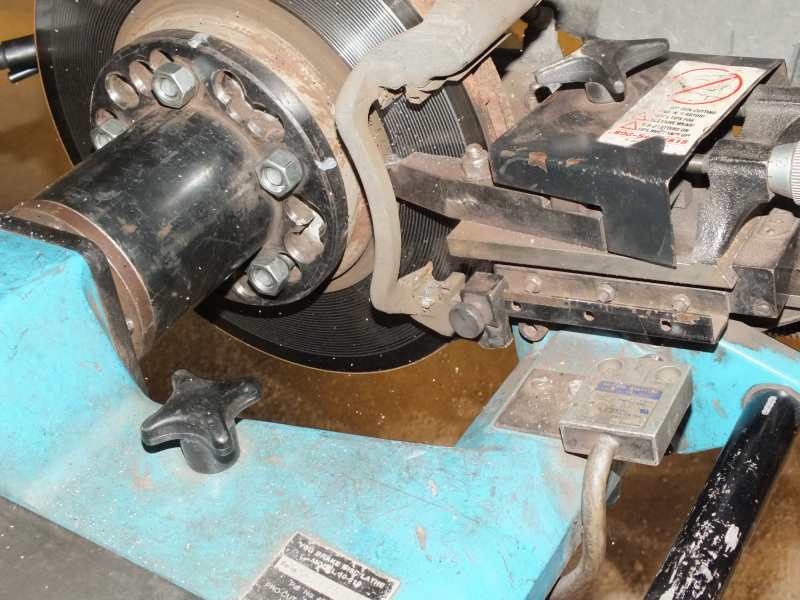
Once his bits are at the center then they will move much more slowly cutting all the metal down evenly as they travel back out to the outside. 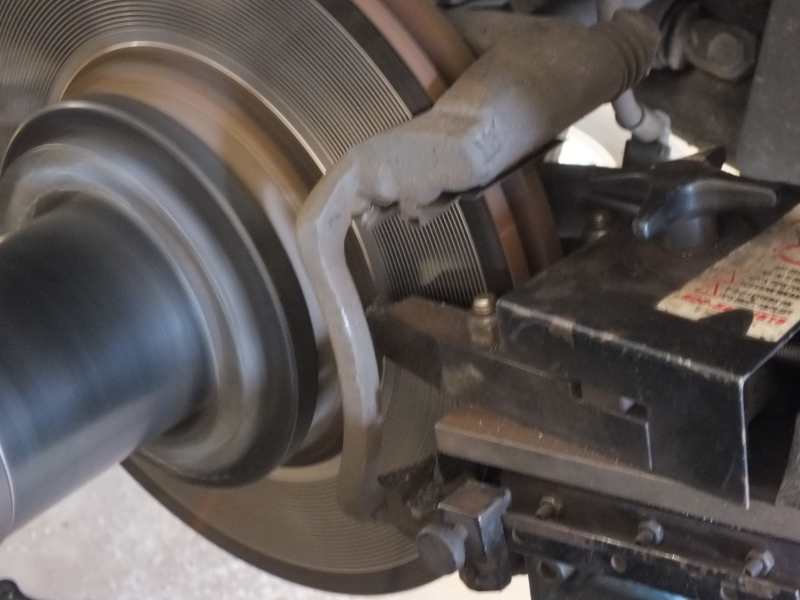
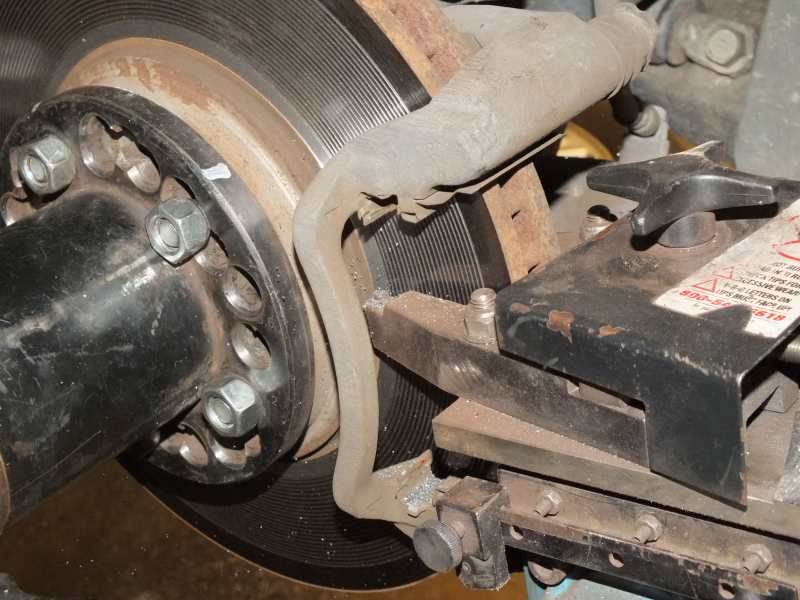
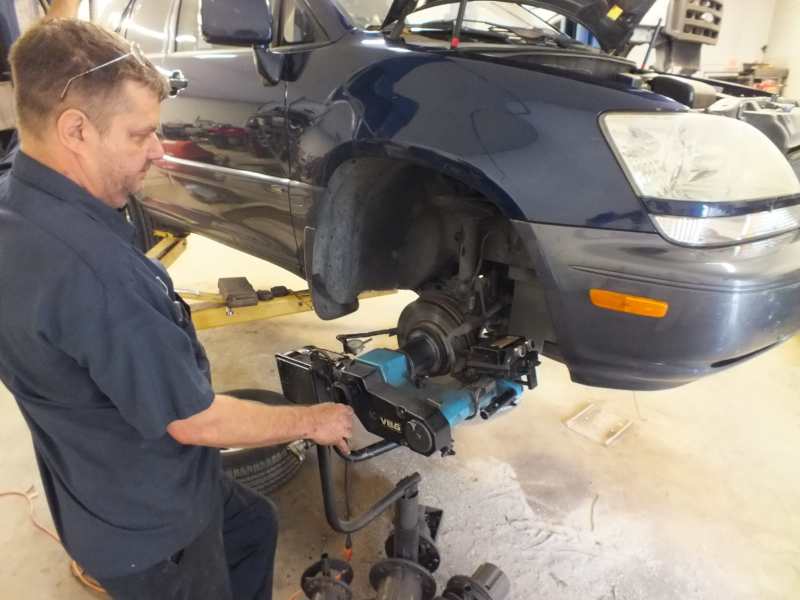
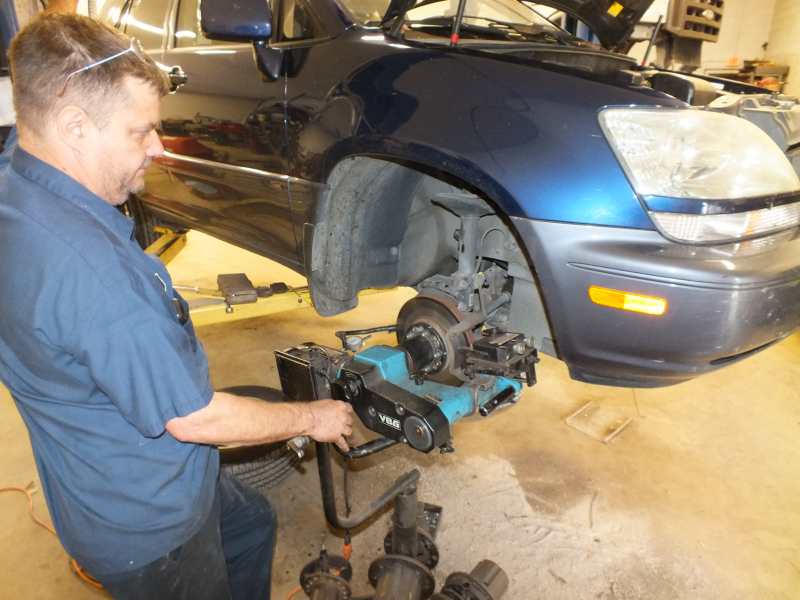
You can see the new smooth surface growing outwards as the bits back out of the rotor. 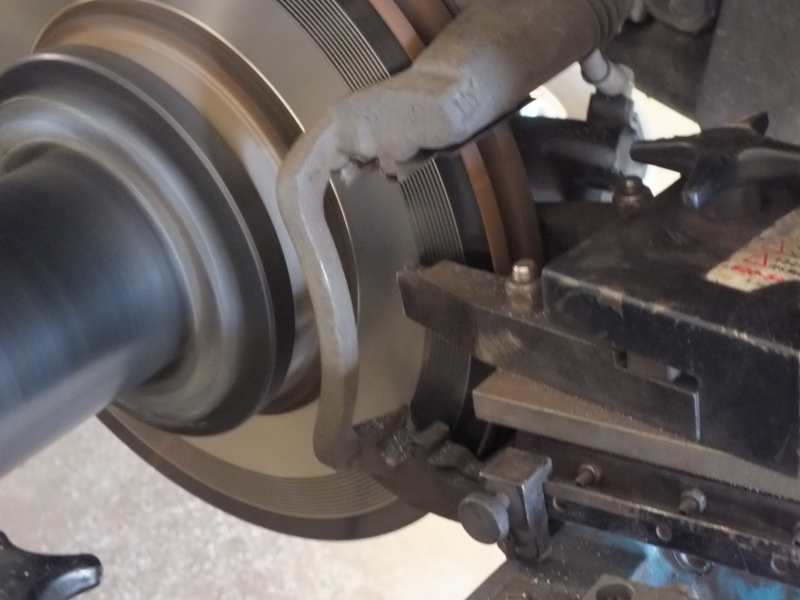
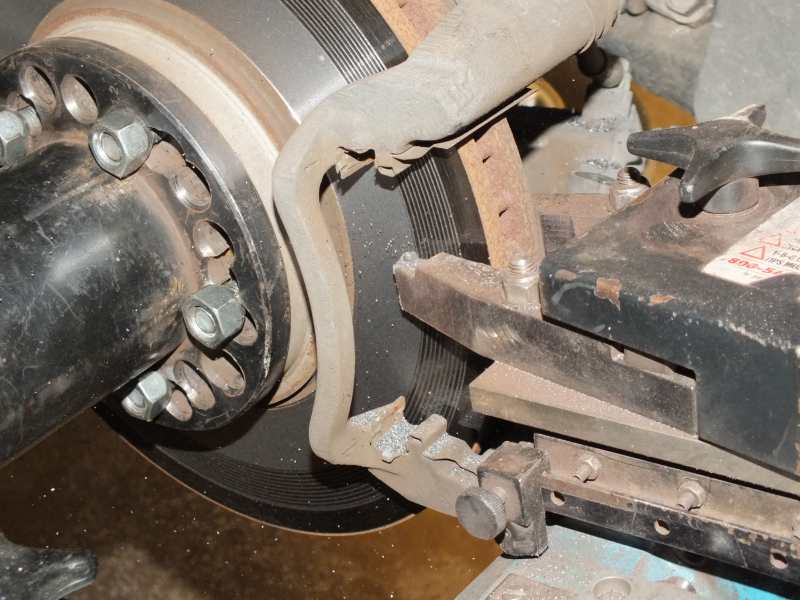
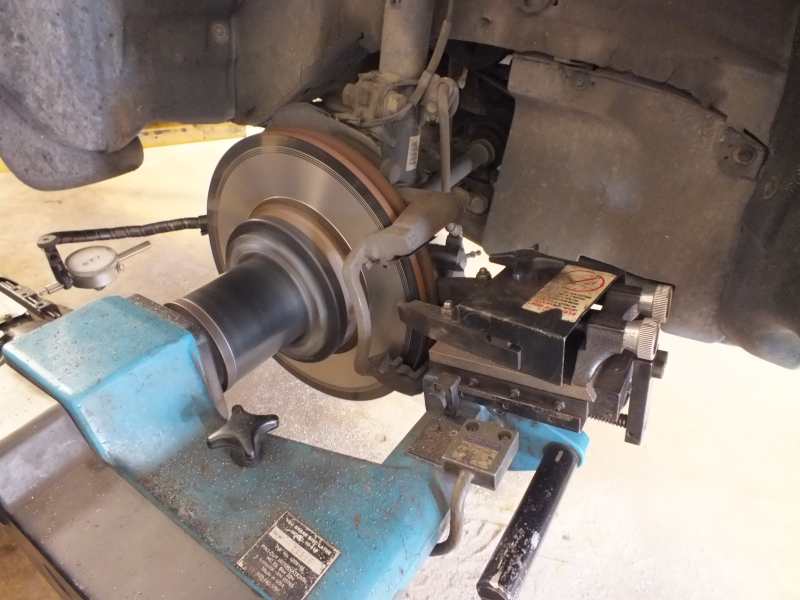
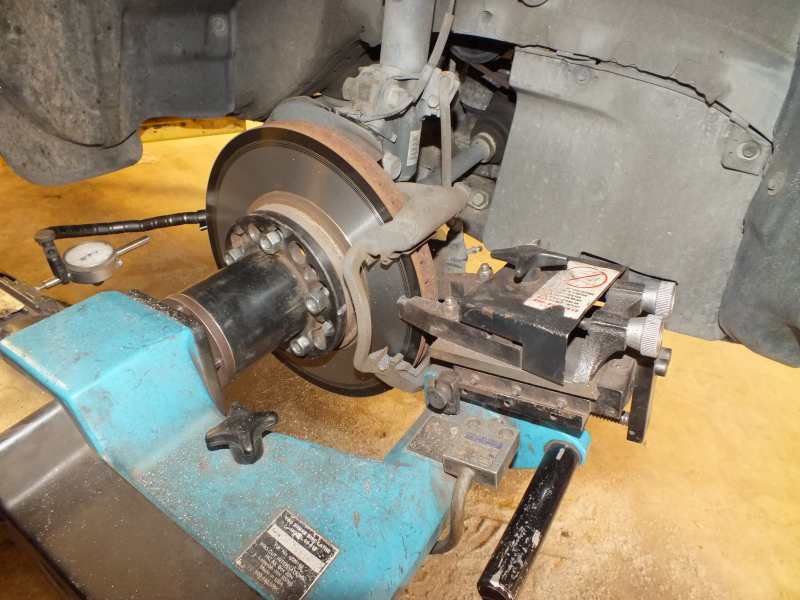
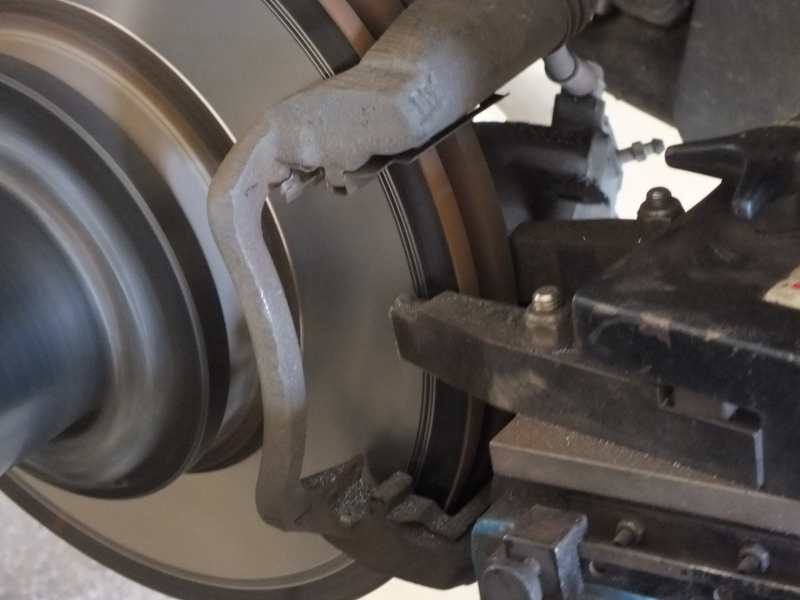
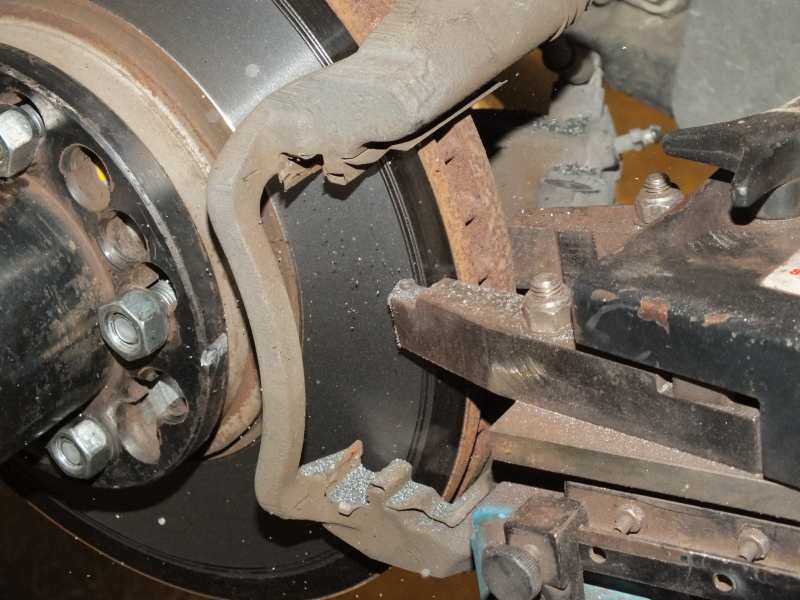
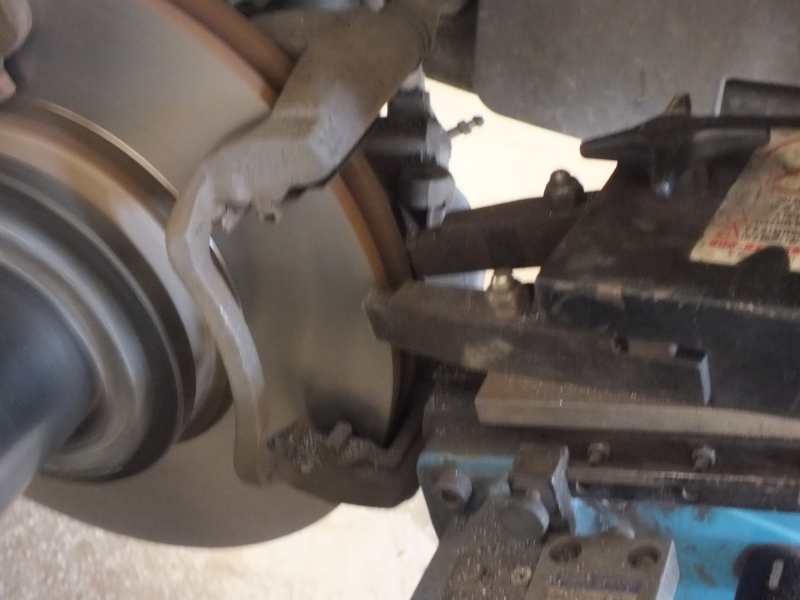
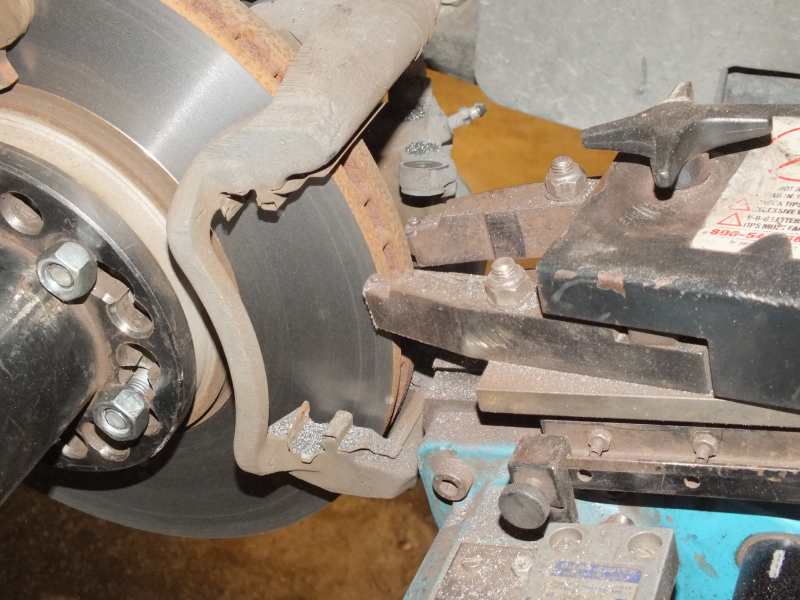
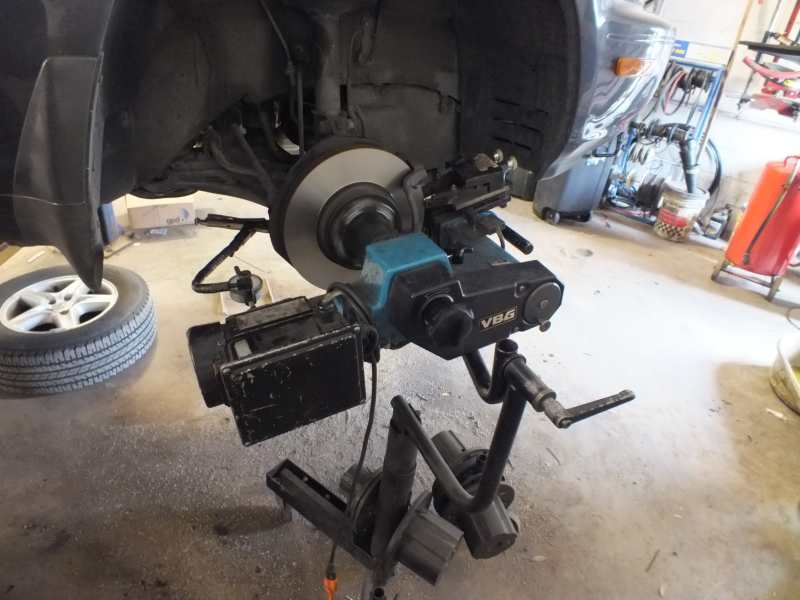
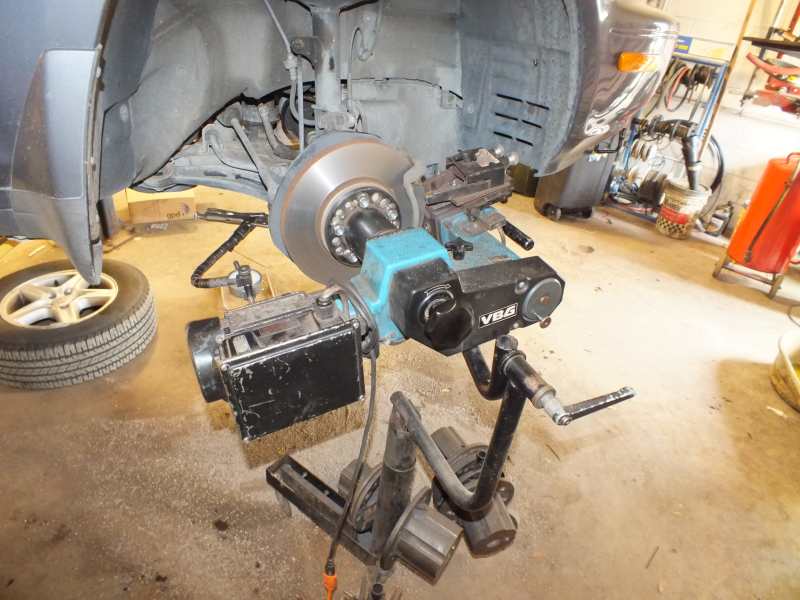
Now here is where we further leave the local machine shops in the dust. After a rotor is freshly cut it can have slivers of metal like slivers in wood. The tiny chunk of metal can still be connected to the rotor in one place but be broken free of the rotor in another place. This loose hanging fragment of metal can create brake noise. Not in all situations but in some. This is why a new brake job can squeak and make noise because it was cut at a machine shop and not on a professional brake lathe by a true brake proffesional. To remove these possible loose fragments of metal, Judd uses an abrasive polishing wheel to remove them before they become trapped inside the brake pad stuck there to forever make squeaking noise. The red arrow shows his air polishing tool that just finished removing any loose slivers. That's why the rotor now has a spiral pattern on it. When you see rotors other shops cut, they don't have that spiral pattern atop of the fresh cut showing they may be leaving the loose slivers there to squeak for you. Do you want to flip a coin to determine if your new brake job is going to squeak? 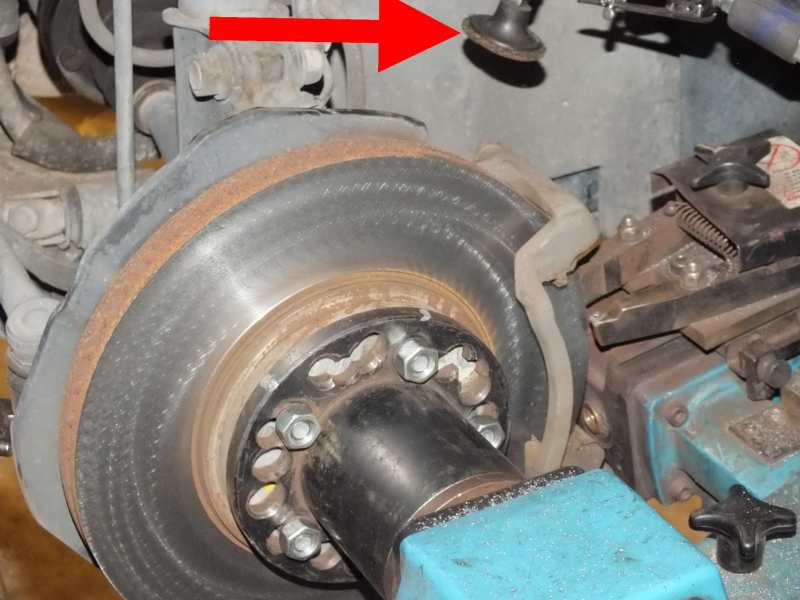
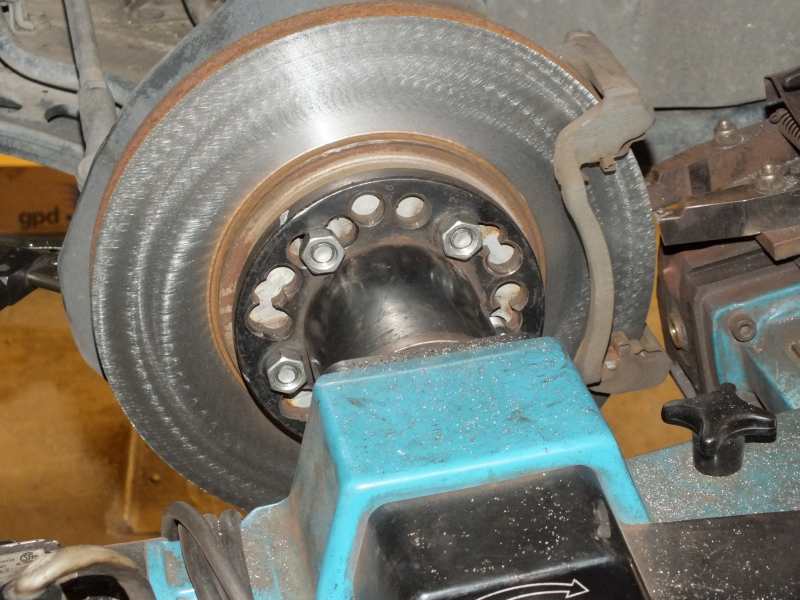
The cutting bit creates slivers all in one direction. The rotating polishing wheel on Judd's air tool rips them off in their weak sideways direction leaving the rotor sliver free and thus guaranteed noise free. 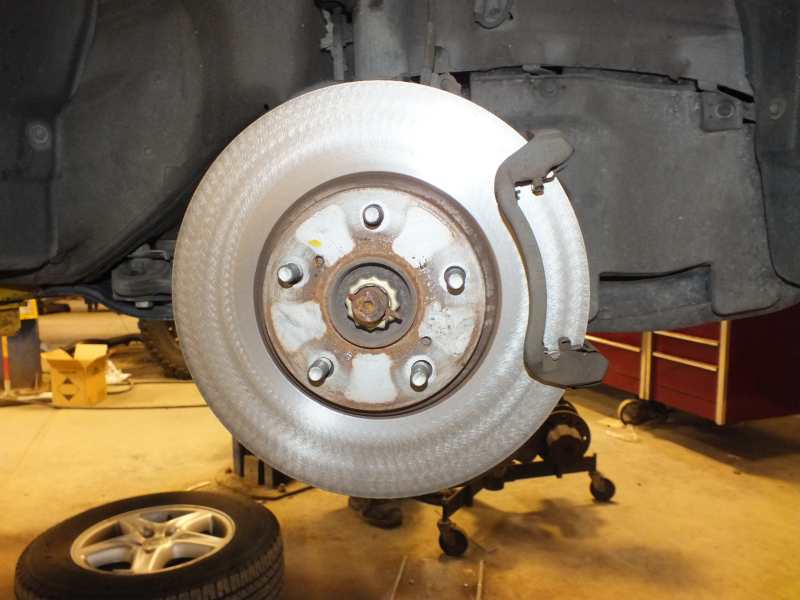
Now he is setting up to do the other side of the car. 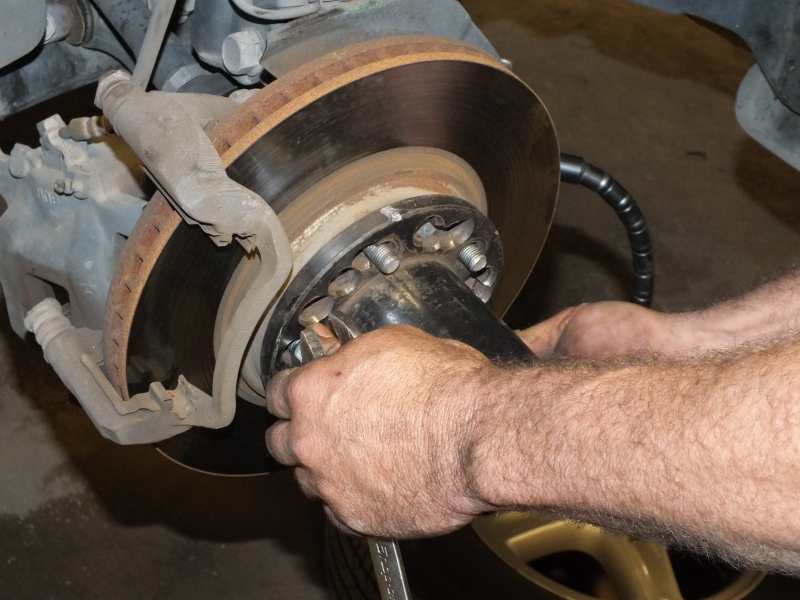
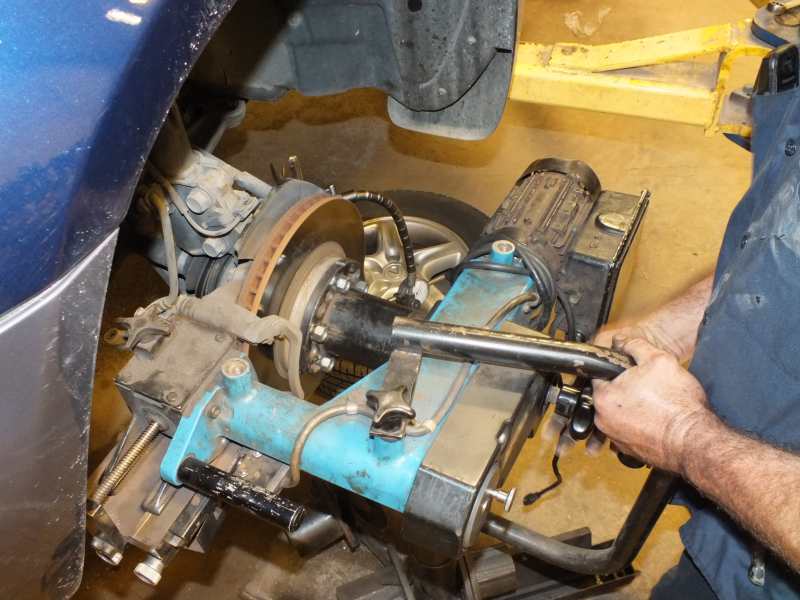
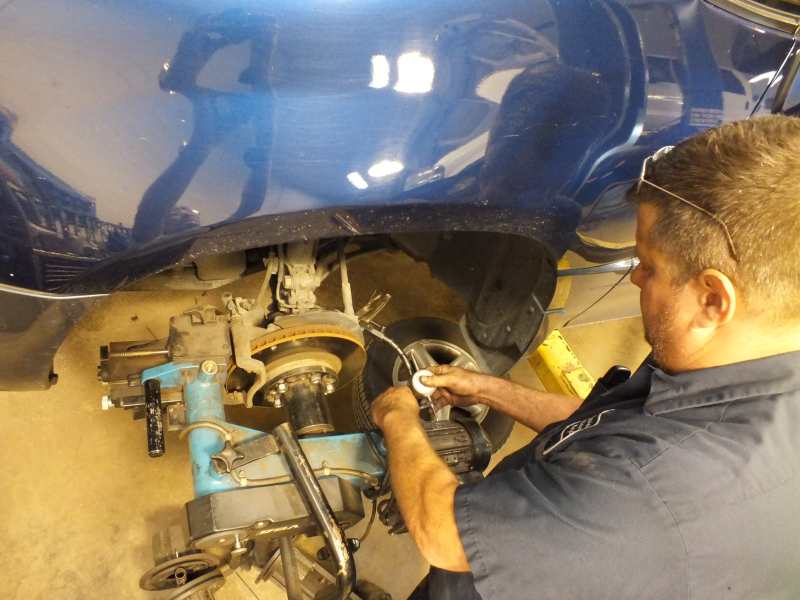
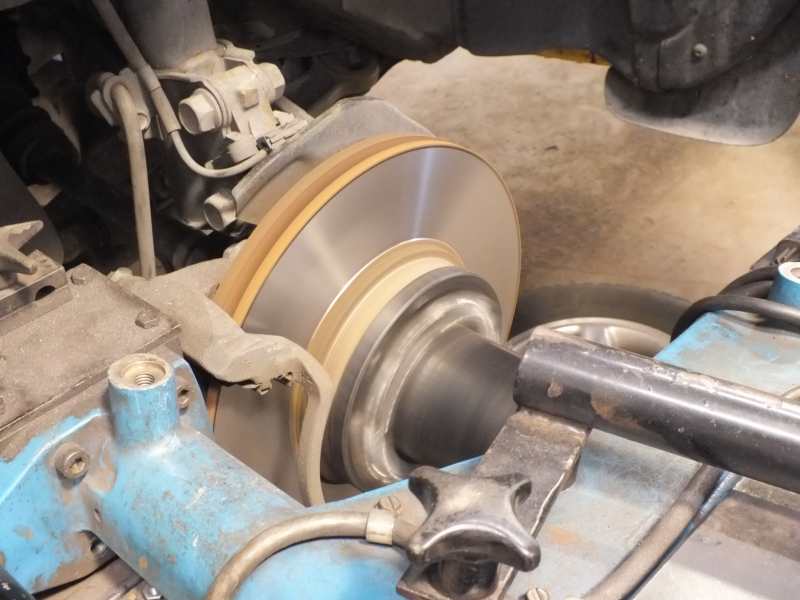
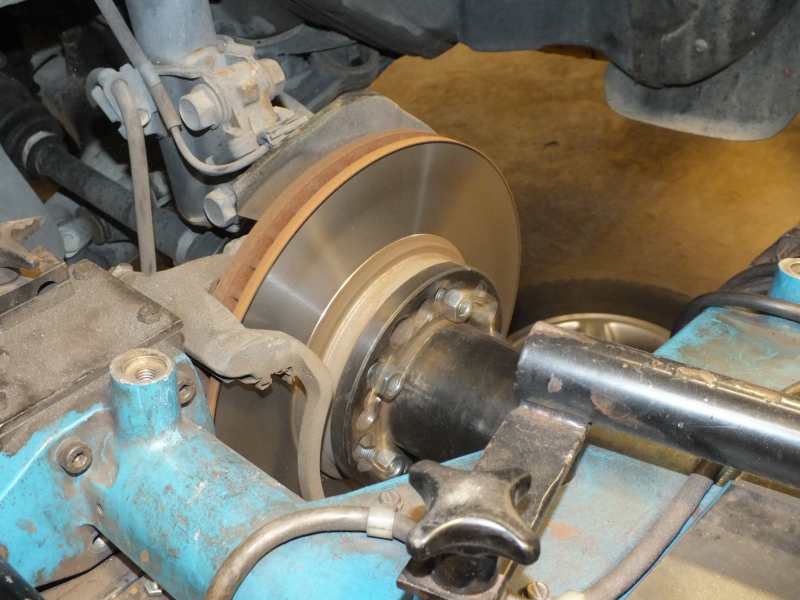
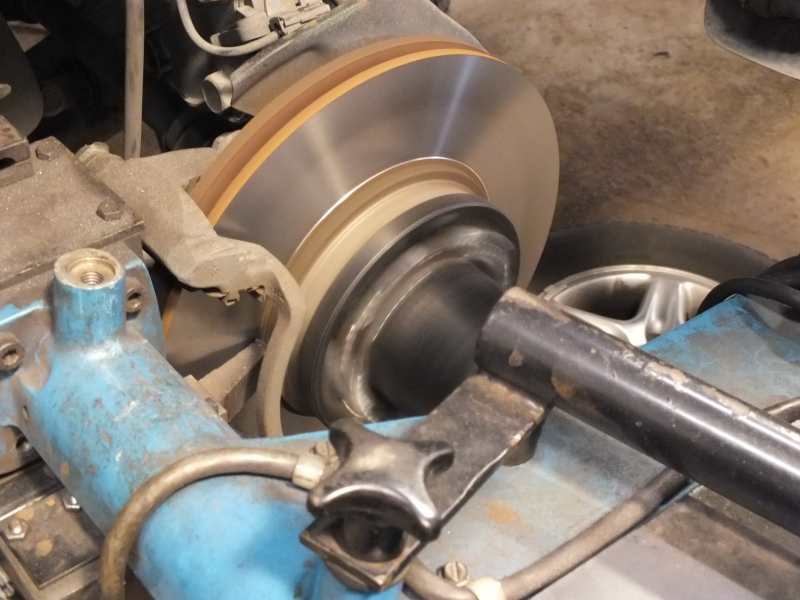
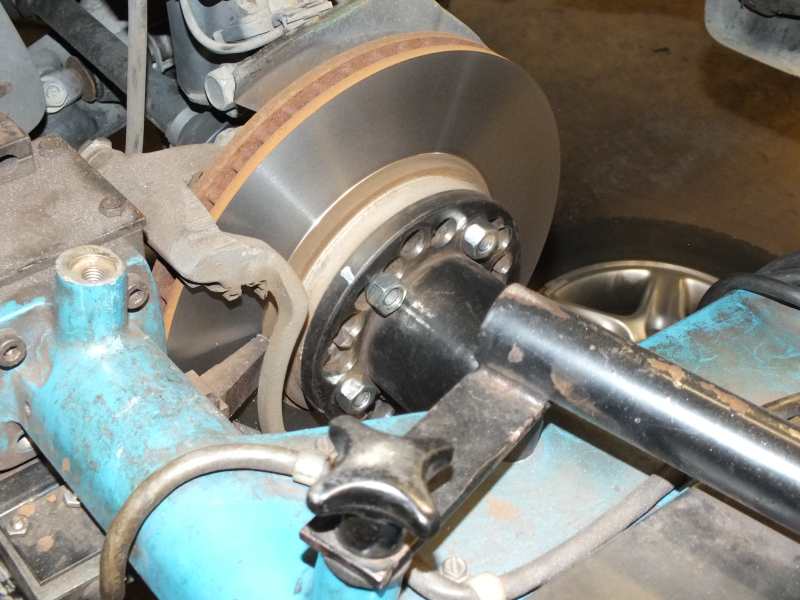
Now you know why Advanced Automotive Repair of Deland Fl does the best brake jobs for the lowest cost and does them so much faster than any other shops. If you have your brakes done at another shop it does NOT mean they will always squeak. But NEITHER does it mean they will always be quiet brakes. Its your gamble, you flip the coin or not. You decide if you want to take the risk of noisy brakes. We are the home of the best auto car brake jobs in Deland Fl and it DOSENT cost more. Call us now to set up your brake repair. (386) 985-2044 |